How Can Intelligent Tightening Technology Solve the Assembly Process Challenges of Automotive Chassis Suspension Systems?
The automotive chassis suspension system is a core component that directly affects vehicle handling, NVH performance, and service life. Statistics show that approximately 40% of suspension system failures originate from bolt connection failures. Traditional tightening processes, which lack precision control, data traceability, and assembly consistency, have become a key bottleneck for automakers looking to improve quality.
Challenge 1: Insufficient Preload Force Due to "Stick-Slip Effect" in Critical Suspension Bolts
Key suspension bolts, such as those for shock absorber struts and control arm connections, can experience the "stick-slip effect," leading to insufficient preload force, loose connections, and in severe cases, bolt breakage causing suspension failure.
Solution: Danikor's high-precision sensor-based tightening tools offer precise torque control to enhance tightening quality, with a full-range torque precision of 3σ±5%. These tools also feature multiple advanced tightening strategies. By setting upper and lower limits for torque, angle, or time, they can monitor slope, torque, angle, and step data during tightening. The tightening curve is dynamically displayed, allowing for timely detection of issues such as floating high and stripped threads. Additionally, these tools have data recording and storage capabilities, facilitating the追溯 of each screw's tightening state and providing robust data support for assembly quality control.
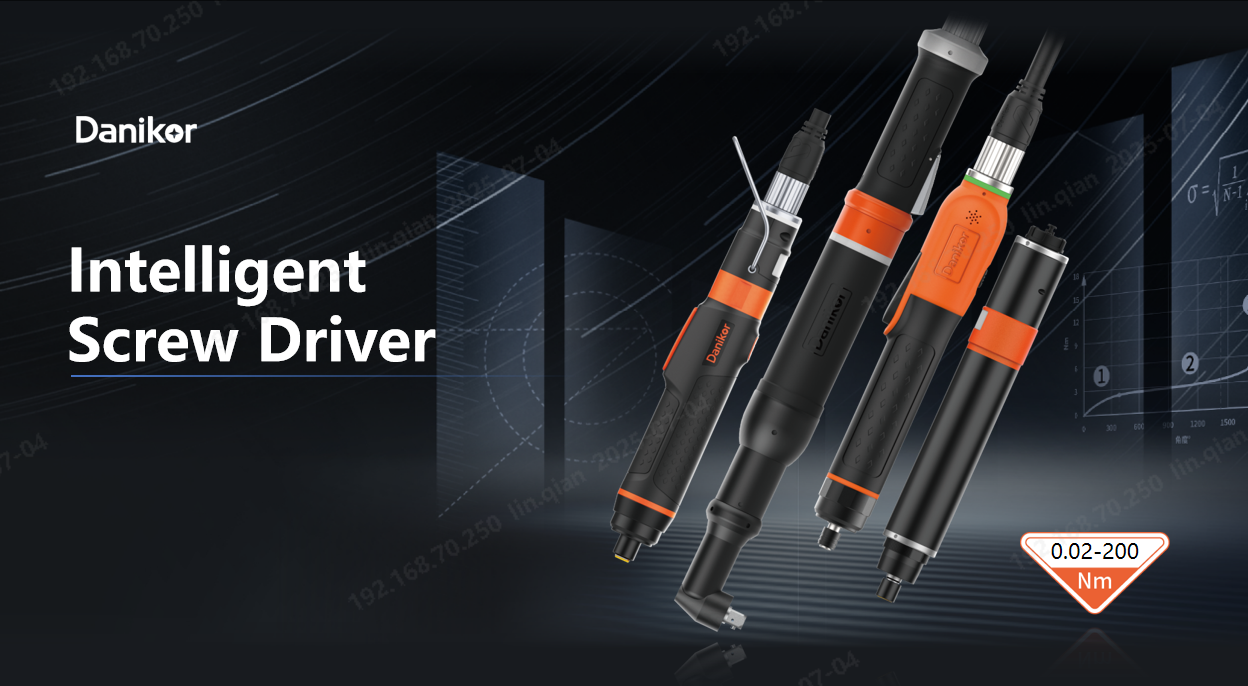
Challenge 2: Complex Assembly Coordination: Subframe Installation Requires Synchronous Tightening of Multiple Points
Traditional tools cannot ensure synchronization when tightening multiple points simultaneously during subframe installation.
Solution: Multi-axis synchronous tightening strategy. When tightening multiple bolts, to avoid the influence of elastic deformation between bolts, a multi-axis synchronous tightening high-level strategy can be adopted. By synchronously controlling the program nodes of multiple bolts, synchronous waiting and stress elimination are achieved during the tightening process, effectively avoiding torque inconsistencies caused by different bolt tightening sequences.
Challenge 3: Poor Tool Accessibility for Hidden Positions: Inner Side Bolts of Shock Absorbers
Tools often tilt during tightening due to poor accessibility to hidden positions such as the inner side bolts of shock absorbers.
Solution: Danikor's bent electric screwdriver is an optimized tightening tool for special spaces. Its 90-degree bent structure allows for flexible operation, enabling it to bypass obstacles and reach into limited spaces for tightening operations, effectively alleviating work difficulties caused by space constraints.