In the auto parts assembly line, screw tightening is a very important link in the assembly process, and it is also a large part of the workload of many stations. Due to the large number of screw types and high similarity, it is easy for employees to make mistakes during operation, resulting in quality problems. According to the quality problem list and repair record table of a certain company, screw slip, screw misloading and screw loose are frequent problems, which are largely caused by repeated tightening, missing tightening and incomplete tightening of employees in the operation process, although the probability of making mistakes can be reduced through certain training and long-term operation. However, due to human limitations, it is impossible to be completely error-free. Therefore, in order to fundamentally solve the problem, it is not enough to rely on strict requirements for employees, but also need to start from the equipment and find ways to achieve full coverage of error prevention functions.
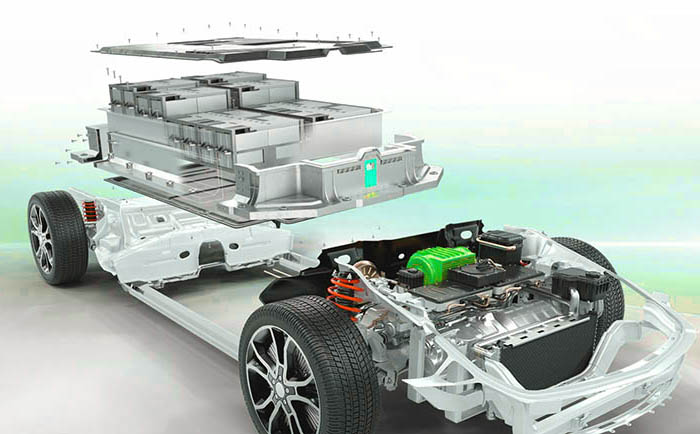
At present, there are many kinds of screw tightening equipment, commonly used is electric tightening tools, because of its high accuracy and stability, in the auto parts assembly station has been widely used. There are many kinds of tightening tools, the common ones in the assembly shop are straight handle tightening tools and gun tightening tools. Among them, the straight handle tightening tool is more suitable for realizing large torque tightening and can work at all angles of the workpiece, while the gun tightening tool is more suitable for realizing small torque tightening and is more convenient to operate in the horizontal direction of the workpiece. A wide range of torque tightening is available for both straight and gun tightening tools, and this feature allows the tightening program to be switched through a bit/sleeve selector. The position of each bit or sleeve on the selector is matched to the corresponding screw and torque
The tightening tool itself has the detection function of output tightening torque, Angle and time, which is the basis of its error-proof control. However, due to the complexity of the production process and fastener coordination, the upper and lower limit monitoring range of these parameters can not be determined by past experience alone, and there is no relevant standard to check, so more efforts are still needed to play the error-proof function of the tightening tool.
The difficulties and solutions of repeated tightening error prevention
To determine whether a screw has been repeatedly tightened, it can be identified by the Angle at which it is turned. Under normal circumstances, the screw from the beginning of rotation to the end of tightening, need to turn several or even a dozen laps, and repeatedly tighten a screw, if the applied torque is the same, then the Angle of the screw will be very small, almost zero. In this regard, it is possible to identify whether a screw is being repeatedly tightened by monitoring its tightening Angle. During the operation, as long as a lower limit of tightening Angle is set to the tightening tool control system, it is detected that the screw rotation Angle is less than the lower limit Angle during the tightening process, indicating that the screw is being repeatedly tightened, and the tightening tool control system will issue a warning. However, two important parameters need to be considered when calculating the Angle of the tightening tool: the fitting torque and the threshold torque. The fitting torque is the beginning of accurate control of the tightening tool, and the torque value cannot be set too small, otherwise it will cause the instability of the tightening speed and the detection data; The threshold torque is the torque at the beginning of the Angle calculation, which needs to be greater than or equal to the fitting torque, and the torque cannot reach the fitting torque most of the time when the screw is tightened, let alone the threshold torque. Therefore, even in the case of normal tightening, the tightening Angle of the screw calculated by the tightening tool is very small, usually less than 100°, which seriously compresses the setting range of the lower limit of the tightening Angle, that is, if the lower limit of the tightening Angle is set too high repeatedly, the tightening tool will be a large number of false positives. Due to the differences in personnel, workpiece and screw material hardness, tightening tool reaction force and whether the washer between the workpiece is soft and hard, the Angle of repeated tightening varies greatly: some are close to zero, and some can reach thirty or forty degrees or even higher. This requires the need to increase the lower limit value of the tightening Angle, otherwise the repeated tightening error prevention function will be useless. From these two opposite constraints, the difficulty of realizing repeated tightening error prevention lies in how to define the lower limit of its Angle. The lower limit angle inferred only by experience and hard parameters are not reliable. To obtain reliable values, it is necessary to go through detailed site inspection and a lot of data analysis. After collecting and analyzing the screw tightening data, the lower limit Angle of the repeated tightening Angle is initially determined. At the same time, the Angle is fine-adjusted according to the wrist force of the field personnel, the material hardness of the screw and the workpiece, the bending straight of the tightening tool, and the thickness and hardness of the gasket between the workpiece.
Leakage tightening error prevention solution
Leakage tightening error prevention is mainly realized by counting function. For example, when a spare part is assembled at a certain station, 10 identical screws need to be tightened, then the tightening tool will accumulate 10 times; If the count is less than 10 times, the production line body or related equipment will respond to restrict the pallet release or alarm; If the count has reached 10 times, the tightening tool locks itself, does not allow the employee to tighten further, and does not unlock until a new workpiece flows in. The realization of this control mode needs to meet two preconditions: first, tighten the gun to support data interaction; Two, repeated tightening error prevention is completely effective.
For the above prerequisite, there are two ways to meet: one is to improve the line body, through the read and write head and tray on the line body to automatically identify different workpieces; The other is to identify different artifacts by manually entering information. For the former method, a read/write head is installed on the wire body, and a marking module (tag) is installed on the corresponding position of the pallet. When each workpiece is put on the line, the employee will write the engine serial number into the tag of the pallet through the read/write head. Since the workpiece is always bound to the pallet on the production line, the serial number on the pallet can be considered as the unique mark of the workpiece. When the tray flows into a station, the serial number information of the front tray will be brushed off, and its serial number will be uploaded through the read and write head, so that the tightening tool can quickly determine whether there is a new workpiece. For the latter method, there is a scanning device beside the line body. The process sequence of this method is: the workpiece flows into the station → the scanning gun scans the bar code/two-dimensional code → tightening the gun controller refreshes the workpiece information → tightening the screw → the counting passes the release → the new workpiece flows into the station. Due to the increase of manual scanning procedures, this method is relatively low production efficiency compared with the previous method. For the latter prerequisite, because the repeated tightening of a screw is mistakenly reported as qualified, then less tightening can meet the counting requirements, as long as the employee does not pay attention to it, it may cause leakage of tightening. Therefore, in order to solve the problem of leakage tightening, it is necessary to ensure that the fault prevention function of repeated tightening is fully realized.
Torque unqualified error prevention solution
The unqualified torque of tightening the station screw is mainly caused by the following points:
(1) The employee loosens the tightening tool switch before it is fully tightened, resulting in insufficient torque;
(2) The speed of the tightening tool is too high, and the inertia is too large when tightening, resulting in torque beyond the qualified range;
(3) For multi-torque tightening tools, because some station sleeves have different torques, it is easy for employees to be confused when choosing sleeves, which causes torque confusion, resulting in over-tightening.
Because the tightening tool itself has a good torque judgment function, the tightening tool will send an alarm signal to remind the employee to correct the mistake when most of the tightening torque is not qualified. However, due to the noisy sound at the assembly site, employees are likely to ignore the alarm information in their rush. Therefore, after the occurrence of unqualified torque, it is necessary to make the tightening tool trigger a more strict and reliable response to restrict the next step of the employee's operation, in order to 100% avoid the occurrence of negligence and omission accidents. The solution is to set up a program in the tightening tool controller, so that the tightening tool alarm function and reverse function are linked together, when the tightening tool controller receives unqualified torque signal, it will trigger the program, that is, if the employee does not reverse the tightening tool, it can not continue to screw down, which can effectively avoid the above (1) and (2) caused by the hidden dangers and risks.
For (3), because the tightening of the gun in the case of the wrong torque will still be "wrong" tightened to the qualified value of the torque, the tightening of the gun will not alarm, so the above error prevention program can not be triggered. In this regard, the sleeve selector should be started by arranging the selection sequence and tightening times of each sleeve according to the technical requirements of screw tightening. The tightening sequence and number of each tightening tool is unique, if the wrong sleeve is selected, the tightening tool will not act, if the number of tightening of a sleeve is enough, the tightening tool can not continue to tighten until the replacement of a new sleeve. This can not only effectively regulate the operation behavior of employees, but also eliminate the quality problems caused by the wrong selection of torque.
The above are several common operational behaviors that may cause quality problems in the tightening process of the tightening tool and the corresponding error prevention program, but the error prevention control in the production process is neither overnight nor once and for all, and it is necessary to formulate an effective control plan according to the quality requirements of the product, and strictly verify the production line periodically according to the control plan. To ensure the long-term effectiveness of the error prevention function.