Based on the production assembly advocated by industry 4.0, The Internet of everything requires a dedicated communication protocol, to gradually open digital and intelligent development, it is necessary to realize intelligent assembly,And pay attention to the digital control and management of the assembly process,.so that the information islands on the original different production assembly lines can realize the "interconnection of everything", And promote the efficient and collaborative development of production assembly.
What is the communication protocol?
To make it simply, all things, when communicating with each other, need to understand each other's language to connect and transmit;
Professionally speaking, the communication protocol, also known as the communication procedure, refers to an agreement between the two parties to the control of data transmission. The convention includes unified provisions on data format, synchronization mode, transmission speed, transmission steps, error detection and correction methods and control character definitions, which must be observed by both communication parties. It is also called link control procedures.
As far as tightening tools are used, there are a variety of communication methods to choose :such as modbus, TCP/IP, RS485, I/O, to ensure that all tightening data is stably collected and transmitted to the client MES system, IT can also monitor and analyze the tightening process, And to improve the efficiency of production assembly.
Fieldbus
Fieldbus is a common application in the industrial field, its simple structure and small amount of wiring, can be quickly assembled and debugging in the field, and the user-defined communication relationship is not only common, but also easy to implement, easy to change, from any place on the network can be configured, debugging and troubleshooting.
It is very suitable for the communication connection between PLC and the field scattered I/O equipment, The simple and effective signaling concept is used to continuously control the field equipment, and the data transmission speed is high and stable.
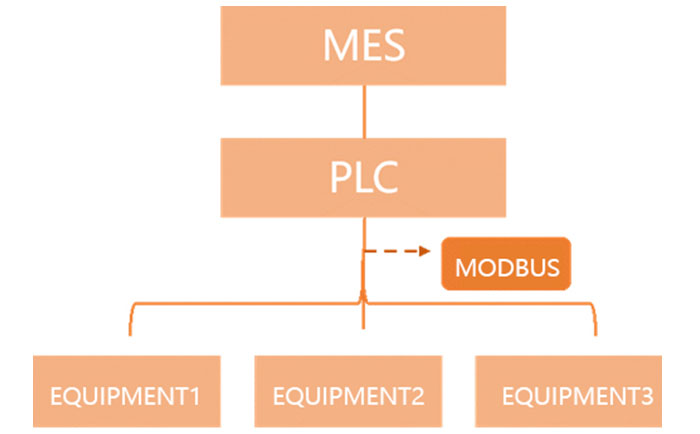
TCP/IP
Based on TCP/IP, it can customize the protocol and has high flexibility. It is suitable for solving the compatibility and interoperability problems of devices from different manufacturers in the control system. It supports the interconnection of devices from different manufacturers and high-speed data transmission through physical network ports to achieve stable real-time transmission of tightening results and curve data.
RS485
RS485 standard is based on RS232 upgrade development, increase multi-point, two-way communication capability, that is, a host with multiple nodes at the same time, It also has a good anti-interference ability, signal transmission distance, And allowing multiple devices to connect, but the transmission efficiency compared to TCP/IP isslower.
I/O communication
Although I/O can also carry out two-way communication, but only transfer the switching quantity, which is suitable for point-to-point communication protocols between field devices, but in the tightening process, the specific tightening value can not be directly collected, So the information feedback has limitations.
With more and more intelligent equipment being applied to the production assembly line, automation and information technology are also constantly running-in. It is necessary to collect, transmit, Record and store the data of various equipment to the MES system through different communication methods, by using this date customer can analyze the transmitted data and predict the trend, and effectively control the tightening process. In addition, it is also convenient for manufacturers to trace on-site assembly problems, maximize the use of data value, and more in line with the development trend of digital and intelligent industrial production assembly.